How to Print on Silk: A Comprehensive Guide for Stunning Results
- ved wangfred
-
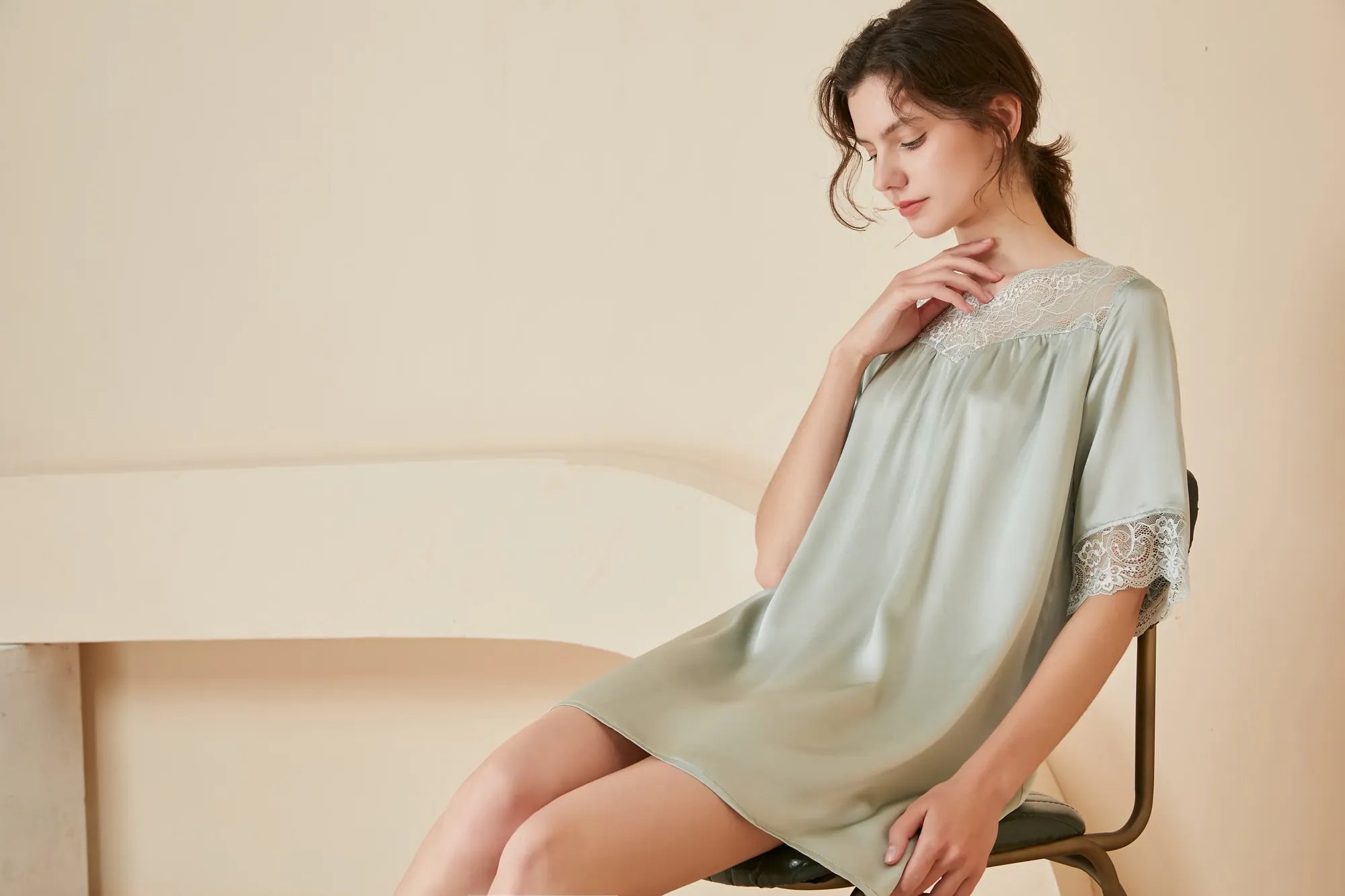
Silk, with its luxurious texture and timeless appeal, has been a favorite medium for artists and designers for centuries. Whether you’re creating custom apparel, home décor, or personalized gifts, printing on silk offers endless creative possibilities. This guide will walk you through everything you need to know to master silk printing, from selecting the right materials to troubleshooting common challenges.
Understanding Silk and Its Unique Properties
Silk is a natural protein fiber known for its smooth surface, vibrant dye absorption, and delicate drape. Unlike synthetic fabrics, silk requires special handling due to its sensitivity to heat, moisture, and chemicals. Before diving into printing, familiarize yourself with the types of silk available:
- Habotai: Lightweight and affordable, ideal for scarves and linings.
- Charmeuse: Heavier with a glossy finish, perfect for garments.
- Crepe de Chine: Textured and durable, suitable for structured designs.
Preparing Silk for Printing
Proper preparation ensures crisp, fade-resistant prints. Follow these steps:
- Wash the Fabric: Remove residual sericin (a natural gum) using a mild detergent. Avoid fabric softeners.
- Choose the Right Ink: Opt for high-quality fabric inks compatible with silk, such as acid or reactive dyes.
- Test Your Design: Print a small sample to check color accuracy and fabric reaction.
- Stabilize the Fabric: Use a temporary adhesive or hooping frame to prevent shifting during printing.
Popular Silk Printing Techniques
Screen Printing
Screen printing is a traditional method ideal for bold, repetitive patterns. Steps include:
- Creating a stencil (screen) for your design.
- Applying ink through the screen using a squeegee.
- Curing the print with heat to set the colors.
Pros: Vibrant colors, cost-effective for bulk projects.
Cons: Time-consuming setup; not ideal for intricate details.
Digital Inkjet Printing
Digital printing offers precision for complex designs. Use an inkjet printer modified for fabric:
- Pre-treat silk with a solution to enhance ink adhesion.
- Load the fabric onto transfer paper or a printer-specific sheet.
- Post-treat the print with steam or heat for durability.
Pros: Photographic detail; minimal setup.
Cons: Higher cost per print; limited to smaller projects.
Block Printing
This handcrafted technique uses carved blocks to stamp designs:
- Dip the block in thickened dye.
- Press firmly onto the fabric, repeating to create patterns.
- Allow the dye to cure naturally for 24 hours.
Pros: Artisanal aesthetic; eco-friendly.
Cons: Labor-intensive; inconsistent results for beginners.
Heat Transfer Printing
Transfer designs from sublimation paper to silk using heat:
- Print the mirror image of your design on transfer paper.
- Use a heat press to fuse the ink onto the fabric.
- Peel the paper away while the fabric is still warm.
Pros: Sharp details; no color limits.
Cons: Requires specialized equipment; may alter silk’s texture.
Troubleshooting Common Issues
- Ink Bleeding: Use less ink or a thicker dye formula.
- Fading Colors: Ensure proper curing time and temperature.
- Uneven Prints: Stabilize the fabric more securely during printing.
Finishing and Caring for Printed Silk
After printing, rinse the fabric in cold water to remove excess dye. Iron on the reverse side using a low-heat setting. Store silk away from direct sunlight to prevent fading.
Ready to transform plain silk into a masterpiece? Experiment with these techniques, embrace trial and error, and let the fabric’s natural elegance elevate your creations. The journey from blank silk to a finished design is as rewarding as the result—every brushstroke, stamp, or digital layer adds a touch of artistry to this timeless material.